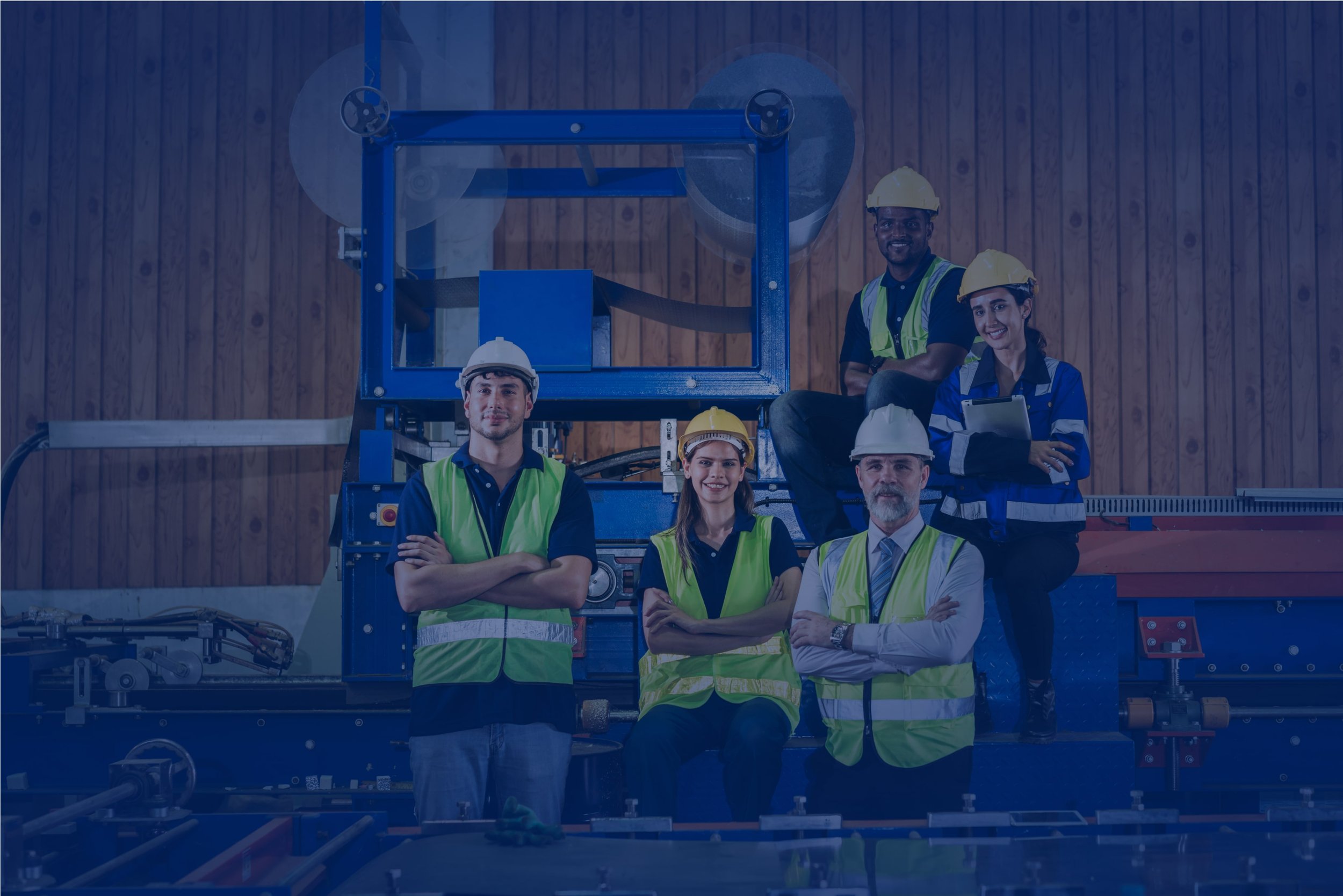
Rules of Flow
Applied Training
Improve Any KPI in Your Operation With Our On-Site Training Program.
Learn Practical Process Flow Improvement Concepts
•
Apply Concepts Directly to High Priority Business Challenges
•
Build Routines That Last Well Beyond the Training
•
Learn Practical Process Flow Improvement Concepts • Apply Concepts Directly to High Priority Business Challenges • Build Routines That Last Well Beyond the Training •
Expected Measurable Results
40% Faster Process Time
30+ Improvements Completed
200+ sq.ft. Freed
What Participants Say
What Is Covered
-
Before the program begins, we collaborate with the business leaders to define a project aligned with business needs and success metrics. We then tailor the training content and activities to the team's goals.
-
Lean Manufacturing
5S & Visual Controls
Theory of Constraints
8020 prioritization
Apply to chartered project
-
KPI visibility
Practice accountability
Data-driven problem solving
Root Cause Corrective Action
Standardization
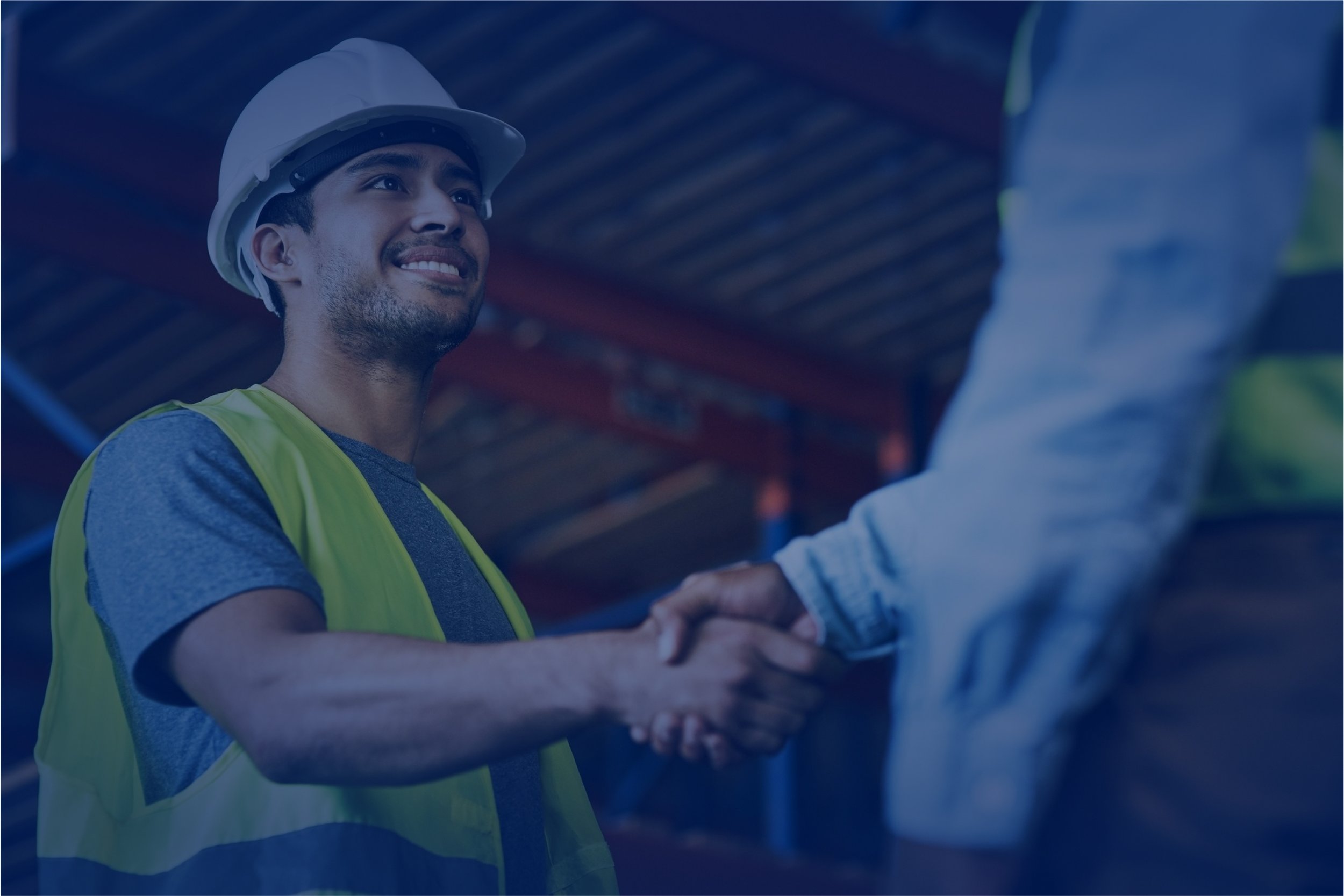
Sample Schedule
Time Commitment:
1 Day a Week, 6 Hour Day (eg. 9:30am-3:30pm), 8 Weeks, Skipping holiday Weeks.
Why Learn From Onsite Lean Works?
On-Site and On-Demand Process Improvement Services
Trusted by Pharma, Aerospace, Aviation and Private-equity
15+ Years Expertise & Lean Six Sigma Leader, Black Belt
Who Exactly Should Attend?
Operations Team Members:
Operators, Leads, Supervisors, Manager Head of Operations.
Included Support Functions:
Planning, Quality, Engineering, Shipping & Receiving, Sales, Finance...
Maximum of 14 Team Members